Man guys. Remember in my last post, when I said Gianna might be the easiest baby we’ve had so far? Unfortunately, I’m eating my words. Sweet girl has been a little fussy while she’s awake during the past couple of weeks and that’s why it’s taken me so long to get this post up…and any post at all. No complaining though and I’m not apologizing because it’s family over blogging but I will say that, while these days are fleeting and I’m trying to soak them up as much as possible, when those days when a routine becomes the norm again come, they will not be unwelcome.
Anyway…
Our DIY, tufted headboard headboard is finito and we are loving it. We have upped the comfort anty 1000% over our previous headboard:

Now it’s behind with the old and in front with the new.


In case you missed it, the tutorial for the tufted back of the headboard can be found here.
The inspiration for the arms of our new headboard was taken from those on this headboard, made by Sarah at Sarah M. Dorsey Designs. I fell in love with the curves at the top of the arms at first sight. She gave instructions on how to make them for the most part, which you can read about in her post about them, and in this post I go into more detail showing how we made them.
Sarah used a 2 x 8 and a 1 x 8 for each arm. We needed a 2 x 10 and a 1 x 10, a tad wider than those Sarah used since we were retrofitting the headboard to our existing headboard. So, instead of getting two boards and screwing them together, we cut costs by using three. (It saved us about $10 to do it this way and the look is no different.)
We used:
1 - 2 x 10 (cut in half lenthwise to make them each about 60 inches long)
1 – 1 x 6 (also cut in half)
1 – 1 x 4 (also cut in half)
The wood shown in the above picture is everything needed for one arm. Like I mentioned above, the boards we bought we had cut in half in-store as they were each 10 feet long and we needed them to be 5 feet long as each arm needed to be 5 feet tall.
We placed the wood together like so to create two, wide arms.

Anthony used wood screws* that were almost as long as the boards were wide to screw everything together. The screws needed to be long enough that they’d securely hold the boards together but not too long that the points came out the other side. 

In screwing the boards together, we had to be careful not to place the screws where we’d be cutting the design out of the top of each arm. If you’re only interested in making two rectangular arms, you won’t need to worry about screw placement.

Once the boards were all one big piece, I labeled each side of the arm – back, front, and top. I did this because the 2 x 10 was slightly deeper than the other two boards put together (you can kind of see it in the above picture) so one side of the arm was flush (front) and the other wasn’t (back). Also, I wanted the 1 x 6 board to be at the front, inside of the arm. In case you would be able to see where the two one-inch boards met through the fabric later, by placing the 1 x 6 board in front, the seam would likely be covered up by the tufted padding of the back of the headboard later. (Turns out that the seam between boards is not noticeable under the fabric at all.)
Next up was creating the curved design at the top of each arm. First, I drew the design on a piece of thick paper and then I traced it onto the wood.

Like Sarah did, I used the lid of a jar to create the rounded parts and then drew a straight horizontal line to connect them. The top rounded part is five inches wide (wider than Sarah’s since we had to accomodate for retrofitting) and the straight line and curve at the front are each 2.5 inches wide.
A good friend of ours cut the design out for me using his jigsaw (thanks Matt!) Anthony has a rotozip he was going to use but the blade wasn’t long enough to cut through both boards. Once the design was cut out, Anthony pre-drilled three holes at back of each arm where they would be attached to the back of the headboard. More on that later.
The next step was wrapping fabric around the inside of each arm so that the arms could be attached to the back of the headboard and then finished. I cut out two rectangular panels of the same gray fabric used on the tufted back – each panel was wide enough to be stapled at the back and wrapped around the entire arm to be stapled at the opposite back and was also long enough that it extended an inch past the ends of each arm on the top and bottom. I used two yards of fabric to finish both arms bringing the grand total in fabric to five yards for the entire headboard.
To start, Anthony laid the fabric on the ground and then placed the wood arm we were working on on top of it, placing it close enough to one edge that there was enough fabric left to be pulled around and stapled. Then he pulled the fabric taught and up and over the other side of the fabric.
(Note: At this point, the insides of the arms needed to be stapled at the back so we had to pay close attention to which side of the wood we were laying on the ground and which side we were stapling.)
Then he stapled the fabric to the back of the inside of the arm.
(Note: You’ll want to make sure the grain of the fabric is straight while it’s wrapped around the arm for a professional look. It should be running horizontally across the side of the arm and/or vertically up and down. As long as you initially cut the fabric panels along the grain, this should be easy to accomplish.)
Here’s what an arm (in this case, the left arm if you’re looking at the headboard) will look like once the inside is stapled:
The fabric will hang loose but will be attached at the back the entire length of the arm.
So that the fabric stayed put while attaching the arm to the headboard, Anthony grabbed a small scissors and stuck the pointed ends into the holes he pre-drilled earlier (the holes that would hold screws that attach the arms to the headboard).

We also realized last minute that we should get the fabric at the bottom of the arms situated before attaching them since we’d be attaching them standing up. To do this, we stapled the fabric at the bottom of each arm to the outside back about six inches up the arm. Then Anthony whipped out his present wrapping skills, folding the fabric like so on the bottom of each arm and stapling it:

I’ll have another post coming later that shows how we attached the new headboard to our existing headboard but at this point in the project, we had the help of another friend (thanks Dan!) to get the arms onto the back. (We didn’t realize how heavy the headboard was going to be so, being postpartum a couple of weeks, I couldn’t help like I normally would.) Basically, Dan held the back of the headboard in place while Anthony held the arms, one-by-one, onto each side of the headboard and screwed them on. Once both arms were attached, they looked like this:

You can see here how the arms and back were held together; where the screws were placed:
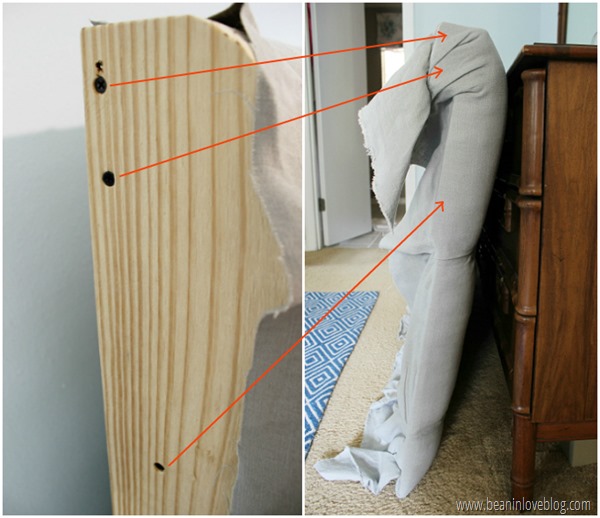
Next, we finished wrapping the fabric around the front and outside of each arm, stapling at the back.

Now it gets a little tricky with the design at the top. To polish off this part, Ifirst folded down the excess fabric at the top of each arm and stapled it to the back.

The arms now looked like this:

Then, I trimmed away the fabric around the design, making sure there was an inch of excess above and beyond the top of the design.
The fabric had to be wrapped onto the design but because of the curves, I had to cut notches around each curve and corner so it could be folded nicely. So, I basically cut triangles with the points almost touching the wood of the arm around each curve and into each corner. I made sure I cut the triangle points deep enough that they’d allow the fabric to be folded without being pulled but not too deep that they went into the side of the arm, exposing the wood beneath.

Next, Anthony helped me staple each flap around the curves down – I held them down tightly and he stapled. (Tip: If a staple doesn’t go in perfectly; if it sticks out a little, just grab a hammer and hammer it flat.)

The last thing I needed to do to finish off the arms was to make a strip of fabric to cover the front of each. To make these strips, I cut out two long, narrow rectangles out of what was left of the fabric we used to wrap the arms in. The front of each arm measured 2.5 inches wide so I cut the rectangles to be 4.5 inches wide so that I could have a finished, one-inch hem on each side. Length-wise, I cut them so that I had plenty of fabric left to be able to fold it over and under the tops and bottoms of each arm. That made them about 70 inches long.
Using my quilting square* was super helpful in making sure I was measuring and cutting straight edges. I drew four lines onto what would be my strips of fabric – two the width of the entire strip pre-hem to show where to cut them out of the fabric remnant and two where I’d fold to make the hem.
To finish the strips, I used no-sew, iron-on hem tape*. I placed the hem tape on the inside of the fold line on one side, ironed it, and did the same to the other side.

To get the strip on its arm, I first cut a small piece of hem tape a little shorter than the width of the front of the arm, placed it at the top of the arm, and ironed on the strip of fabric so that it was secured by the hem tape.


I wanted to glue most of the strip on because I wasn’t sure I had enough hem tape to iron it on so by placing that small piece of iron-on tape at the top, the strip was held in place and allowed the glue I used to dry without moving. I did the same thing with a small piece of iron-on tape to the flat part between the two curves of the design at the top of each arm and also placed one right below the second curve; right on the front, flat part of the arm.
To glue the strips on, I ran two small lines of glue down the middle sides of each side of the front of the arm like so:
(I used this fabric glue but any craft glue and even hot glue will work. Hot glue just requires a lot of careful gluing so it doesn’t get on the fabric where it’d be tough to remove.)
I did it this way all the way down. There was extra fabric at the bottom of the arms that we just folded under the arm – I folded under while Anthony held the headboard off the ground. One day, when we move and have to take the bed apart, we’ll staple them down but until then, no one will ever know they’re not secured underneath so shhhhh…
Ta-daaaaa! That is IT!

It cost us a little under $100 to make this headboard and if we’d have had to buy the foam for it, it would still only have rung in at around $130. Not too shabby, eh? Not too shabby at all. :D

Right after we finished it, I got really excited and quickly cranked out two new pillow covers for the euro pillows on the bed plus some matching faux roman shades that you might’ve noticed. I stole the smaller square pillows from the living room to add some more color but really I’m still sulking over the fact that the fabric I wanted to make covers out of for those costs $230 PER YARD. No way Hosea. It’s this orangerie floral by Designers Guild…
…and if I ever find a remnant that is majorly, and I mean majorly discounted, I will pounce. Until then, I’ll forever (but hopefully not) be on the look-out for a similar print and pattern.
So, the headboard is done but what about the footboard? Well, eventually I’d love to sand and restain it and I’m toying with the idea of upholstering and tufting the flat part in between the two posts but for now, there are bigger project fish to fry in this casa but don’t be suprised if that post pops up one day in the future.
There are still a lot of things I want to get done in our room before we call it “done” – painting and adding legs to the nightstands, painting the dressers, painting or restaining our desk and bookshelf, hanging stuff on the walls, making a West Elm chandelier knock-off that I’ve had on the agenda for over a year now, blah, blah, blah… Basically, the room will see it’s final state in a few years at the rate we move. So it goes and so it is.
But, now that I have a plush surface to sink my spine into when stress strikes, I don’t care how long it takes. Slow and steady wins the home decor race…or maybe that’s just an excuse for decoristas with kids. ;)

Stay tuned for a quick post on how we attached this headboard to our existing, thrifted bed frame.
Adios. :)
*Affiliate link to product we purchased or something similar to what we purchased to make this headboard. If you click and buy, we will get a small commission. Thank you for helping us keep the lights on around here! :)
. . .
